Hot Products
About Us
Foshan Nanhai Jiawei Metal Products Co., Ltd. has a history of more than 30 years since its establishment in 1992, with strong economic strength. With the rapid development of business, the production scale has also been expanding. In the second half of 2001, the new plant began to be built, and was completed and put into operation in 2003. Now the company covers an area of 21800 square meters, including 9500 square meters of factory buildings, 780 square meters of office buildings and 2780 square meters of dormitories. There are 165 employees, including 46 engineers and technicians.
More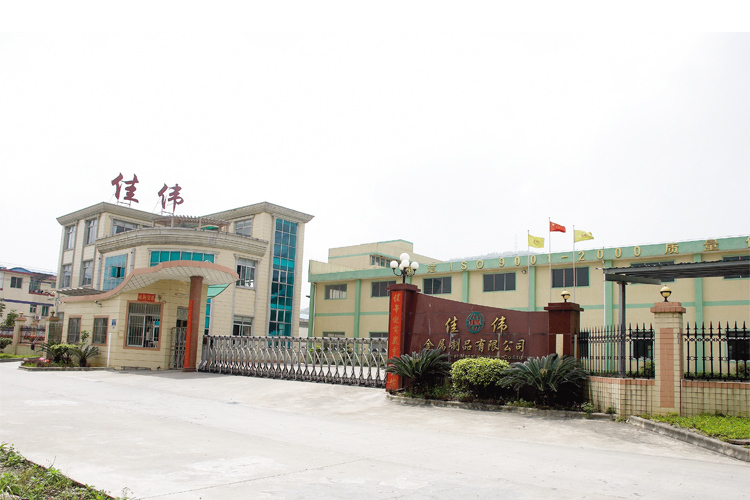
News
-
05/05-2024
Innovative Non-Toxic Cookware Revolutionizes Culinary ExperienceIn the dynamic culinary industry, manufacturers are responding to the demand for safe and efficient cookware. Aluminum die-cast and non-stick cookware, alongside BBQ accessories and Teflon pans, are at the forefront. The quest for the best nontoxic nonstick pan has led to revolutionary advancements. Our company leads this charge with premium nontoxic nonstick cookware, boasting durability, safety, and performance. From aluminum die-cast durability to superior non-stick coatings, our products redefine culinary excellence.
-
09/04-2025
Die-Casting Industry’s Dual Breakthroughs: Surging Demand for Die-Cast Components Drives Die-Casting Mold InnovationIn 2025, the global die-casting industry enjoys dual dividends of "demand explosion" and "technological iteration." New energy vehicles (NEVs) and other sectors drive the die-cast components market to exceed $320 billion, while die-casting molds upgrade via AI and new materials. NEVs use over 50kg of die-cast components per vehicle; Tesla’s Model Y integrated die-castings boost efficiency, and LK Group launches 9,000-ton die-casting machines with supporting molds. Mold tech breaks through in materials (ceramic-coated steel, composite molds) and intelligence (AI design systems). Green manufacturing also gains traction. By 2030, the integrated die-cast components market is expected to surpass $80 billion, with the "intelligence + green" path fueling industry growth.
-
08/27-2025
Die-Cast Components Industry: Innovation-Driven, Ushering in Explosive Growth and Profound TransformationThe global die-cast components market is booming, projected to hit $320B by 2025 (35% up from 2023), driven by NEV lightweighting and integrated die-casting tech. Aluminum/magnesium alloy die-castings cut NEV weight by 30-50%, with Tesla, BYD partnering suppliers to boost usage. Integrated die-casting slashes costs/processes but faces high alloy prices and low yield rates (e.g., Tesla’s early Model Y floor yield <60%). Firms innovate via new alloys (e.g., Lizhong’s high-strength ones) and tech (9,000T machines, AI-controlled processes, vacuum die-casting). By 2030, NEV die-cast usage may top 60%, with integrated die-cast market set to exceed $80B.